Organizing your shop so that it runs safely, smoothly and efficiently does more than make for a better workplace – it can actually have a measurable effect on your bottom line.
by Paul Reed
Most enlightened shop owners won’t dispute that a well-organized shop runs better, is safer and is an all-round more pleasant place to work. But in many cases, the reality runs short of the ideal.
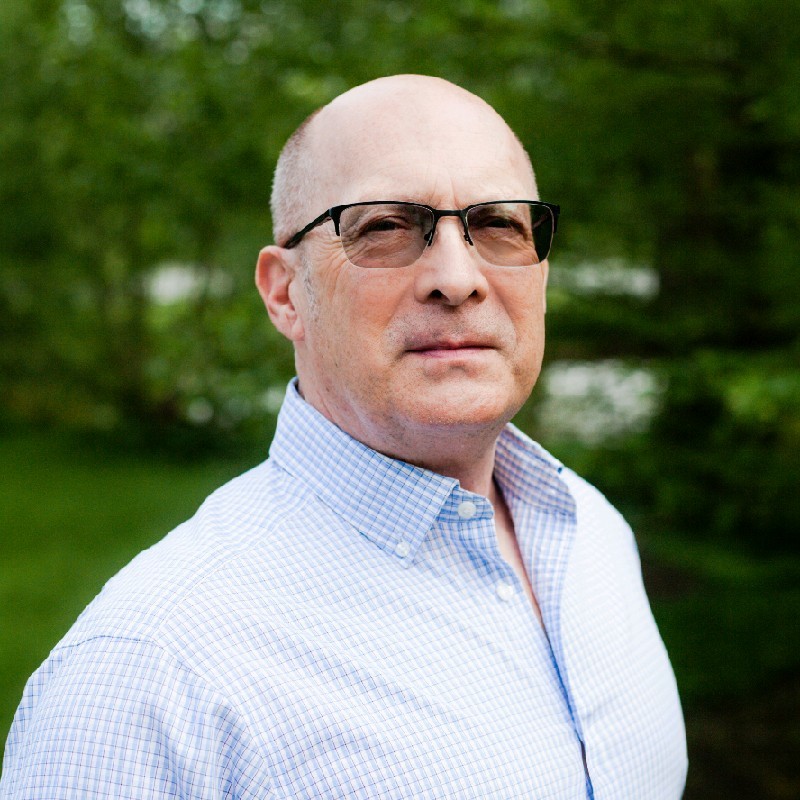
The Showroom Guy
Retail Environment Solutions
www.theshowroomguy.com
Perhaps the shop has grown too quickly over the years, and in order to squeeze in another hoist, every bay is just a little tighter than is ideal. Or perhaps there was once a workable organizing principle to the shop, with well-planned systems and rules in place, but over time people have gotten less diligent about keeping things in order.
But keeping the shop organized is more than a matter of efficiency. It’s also a matter of safety, and it can actually affect your bottom line.
Let’s do some math. Say your tech spends an extra two or three minutes per repair order digging around for the right tool, or walking all the way to the other end of the shop to pick up the part he needs and then waiting for the parts to be picked by the parts person. If the tech works on 6 cars a day, that equals 18 minutes per day per technician lost. Multiply that by 5.5 days a week you are open for service. Let’s say you have 4 techs x 18 min per day each x 5.5 days open…that equals 396 min lost per week. Then divide that by 60 min per hr. = 6.6 hrs. lost per week. If your door rate is $110 per hour, that equals $726 per week. Then conservatively, let’s say you are open 49 weeks a year. This is when it gets crazy…That’s $35,574 of lost revenue, and that’s being conservative.
Let’s turn that around the other way: suppose everything the tech needs is close at hand, right where and when he needs it to be. On a brake job that’s rated at two and half hours, if the tech can streamline the job down to two hours or one and a half, that’s a full billable hour added to your bottom line. That adds up pretty quickly, too.
The best organized shops start out that way form the beginning. As shop designers, we consider creating an efficient work layout as the first priority when we lay out our floor plans, with “zones” for each working area of the shop, adequate room for each bay, and work and supporting areas arranged around them logically and conveniently. But there are steps you can take to in improve flow and efficiency, even if you aren’t ready yet for a major reorganization of the entire shop floor.
The most important first step is to closely examine how people move in, around and out of the space, and how cars enter and exit the bays. Safety should be your number-one priority, of course; and that means ensuring there is adequate space between bays for techs to move and work without feeling cramped, that sightlines are clear wherever vehicles are in motion, that lighting is bright and makes it easy to see what you are doing, and that there is enough room between hoists to wheel portable equipment like testing equipment in and out easily.
Ventilation hoses and other pull-down equipment should be located easily within arm’s reach and convenient to use and put back when not needed. (I’ve heard of situations where the ventilation equipment was such a nuisance to hook up that the techs often skipped that step for quick jobs, which is not only illegal but dangerous.)
The location of parts pick-up stations, or the hub where the techs obtain the parts orders for a particular job, can be another bottleneck. In a smaller shop, having one central part hub or perhaps one on each side of the shop is probably adequate. But in a larger centre, aim to have at least a small parts station for every 8 to 10 bays.
Think that seems like a hassle? The time a tech spends walking across the shop to pick up the part he needs – not to mention the natural human inclination to stop for a couple of minutes and chat with a buddy as he goes by – then to line up behind other techs before obtaining his part, is time spent not working on a customer’s vehicle.
Some large dealerships will have actual vending machines placed close to the bays that dispensed small, frequently used parts like spark plugs, clamps, bulbs, and so on. It is a real convenience that can save the techs a few steps for these little nuisance items, and they will appreciate it.
Organization also works at the micro level. Let’s have a look at the tech’s toolbox. Every licensed mechanic has, or should have, a good-sized, secure workstation with multiple drawers and cabinets. One commonly used organizing system is to use one drawer for each type of tool, with tools lined up side by side, smallest to largest, left to right. (You can get rubber drawer liners that keep the tools from rolling around when the workstation is moved; the liner also protects the tools and the drawer interior from damage.) Laying the tools out neatly like this prevents accidental misplacement of tools, and makes it easy for the tech to instantly put his hands on exactly the tool he needs.
Some techs may have their own organizing systems for their tool sets, and if it works for them, great. I used to work at an Acura dealership, where we worked basically on just three vehicle models and did the same basic service over and over. One of my colleagues had a dedicated drawer in his workstation with everything he needed for just that basic major service: the right lug wrench, spark plug tapper, etc. We kidded him that it was a bit OCD, but it probably shaved several minutes off the time he spent on each car.
Once the shop is well-organized and running smoothly, the onus is on you, the owner (or the shop floor manager if there is one) to ensure that organizing systems are maintained daily. Ensure everything is put back in its place when the service is done, and that the shop is kept spotless and tidy, at least by the end of the day.
Some aspects of staying organized may seem small or even fussy – like mom nagging you to pick up your room – but when you come down to it, few aspects of daily life at the shop are more important. That’s not only from the point of view of safety and efficiency, but in direct, measurable effects on your bottom line.
This is well written and can be applied to all aspects of business from repair and race shops to a contractors work area.